Introduction 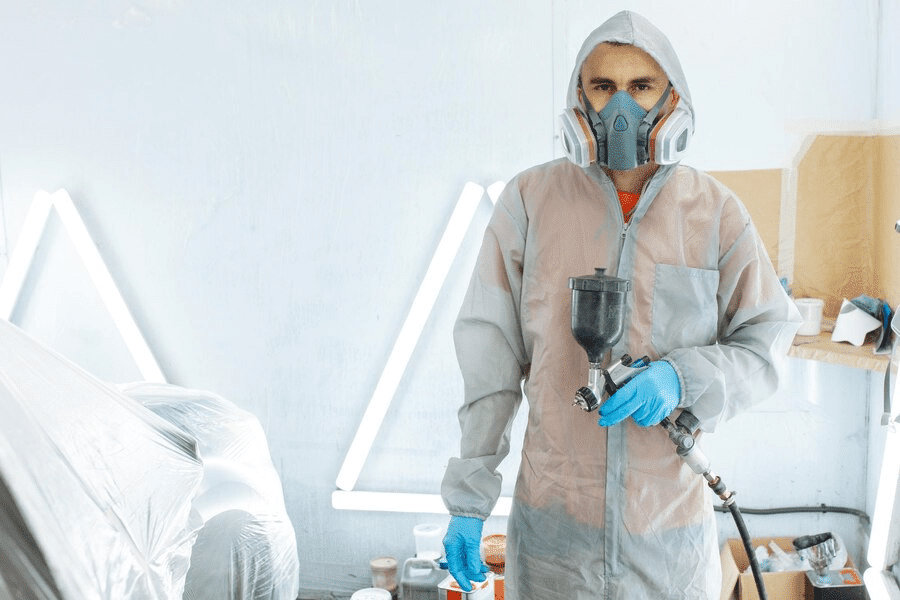
Coating inspection plays a crucial role in ensuring the durability and functionality of structures and products. It ensures that the applied coatings meet specific requirements, protecting against corrosion, wear, and environmental factors.
Coating inspectors are the guardians of quality. They oversee coating application processes, verify compliance with standards, and identify defects. Their role is pivotal in upholding quality standards and ensuring the longevity of coatings.
Fundamentals of Coating Materials and Processes
Types of Coating Materials
Coating materials are substances applied to surfaces in a thin layer to protect, enhance appearance, or provide specific properties. There are various types of coating materials, each with unique characteristics and purposes:
- Paints: Paints are a common type of coating material made of pigments, binders, solvents, and additives. Pigments provide color and coverage, binders hold the pigments together and adhere to the surface, solvents help with application, and additives improve properties like durability and drying time.
- Primers: Primers are coatings applied before the main coating to enhance adhesion, corrosion resistance, and overall durability. They often contain rust inhibitors and other additives to prepare the surface for subsequent coatings.
- Powder Coatings: Powder coatings are dry, free-flowing powders typically composed of polymer resin systems, curing agents, pigments, and additives. They’re electrostatically sprayed onto a surface and then cured to form a durable, protective, and visually appealing coating.
- Coatings for Specialized Purposes: There are coatings designed for specific applications, such as fire-resistant coatings, anti-graffiti coatings, anti-fouling coatings for marine applications, and more. These coatings are tailored to provide specific properties required for their intended use.
- Galvanic Coatings: Galvanic coatings involve the application of a sacrificial layer of metal, such as zinc, to protect the underlying metal from corrosion. This type of coating utilizes the principle of galvanic corrosion to safeguard the substrate.
Coating Application Techniques
Coating application techniques refer to the methods used to apply coating materials onto a surface effectively and uniformly. Proper application is critical to achieving the desired coating properties and appearance:
- Spraying: Spraying is a common technique involving the use of spray guns to atomize the coating material into fine droplets. These droplets are then directed onto the surface to create an even coating. Techniques include airless spraying, air-assisted spraying, and electrostatic spraying.
- Rolling and Brushing: Coating materials can be applied using brushes or rollers. Brushes are typically used for smaller areas or intricate details, while rollers are more efficient for larger surface areas. This technique is effective for achieving a smooth and consistent coating.
- Dipping: Dipping involves immersing the object or surface into a tank or container of coating material. The coating adheres to the surface upon removal, providing an even and complete coverage. This technique is often used for small, easily submerged items.
- Electroplating: Electroplating is a process where a metal coating is applied to a surface using an electric current. The surface to be coated is immersed in an electrolyte solution containing the metal ions, and the electric current causes the metal ions to adhere to the surface, forming a coating.
Surface Preparation for Coating
Surface preparation is a crucial step to ensure the adhesion, durability, and quality of the coating. Properly preparing the surface before applying the coating involves several key steps:
- Cleaning: Remove any contaminants such as dirt, grease, oil, rust, or old coatings from the surface. Cleaning can be done using solvents, alkaline cleaners, power washing, or abrasive blasting.
- Degreasing: Eliminate any oily or greasy substances that can hinder adhesion. Degreasing is typically achieved using specialized degreasing agents or detergents.
- Abrasive Blasting: This process involves propelling abrasive particles at high velocity onto the surface to remove old coatings, rust, and other impurities. It also creates a rough surface profile, enhancing adhesion of the new coating.
- Etching: Etching involves creating a slightly rough surface by using chemicals or mechanical means. This improves the adhesion of the coating by providing a better surface for the coating material to grip onto.
- Priming: Applying a primer or a pre-treatment coating helps in enhancing adhesion, corrosion resistance, and overall durability of the final coating. The choice of primer depends on the substrate and the type of coating system being used.
Coating Inspector Standards and Regulations
Overview of Industry Standards
Industry standards refer to a set of criteria and guidelines established by industry organizations, professional bodies, or regulatory agencies to ensure the quality, safety, and performance of coatings in various applications. These standards provide a framework for coating materials, application processes, testing, and evaluation. Examples of industry standards related to coating inspection include:
- AMPP International Standards: AMPP (Association for Materials Protection and Performance) develops standards related to corrosion control and coatings. These standards cover surface preparation, coating selection, application methods, and inspection procedures.
- SSPC (Society for Protective Coatings) Standards: SSPC develops standards for surface preparation and coating application to ensure durability and performance in different environments.
- ASTM International Standards: ASTM develops standards for materials, products, systems, and services across a wide range of industries. In the context of coatings, ASTM standards cover testing methods, material specifications, and performance requirements.
Compliance with Environmental and Safety Regulations
Compliance with environmental and safety regulations is crucial in the coating industry to minimize the environmental impact and ensure the safety of workers and the public. Coating processes can involve hazardous materials, so adherence to regulatory guidelines is essential. Some aspects of compliance include:
- Environmental Regulations: These regulations govern the use, handling, and disposal of coating materials to prevent environmental pollution. They may include restrictions on volatile organic compounds (VOCs), hazardous air pollutants (HAPs), and proper waste disposal procedures.
- Occupational Safety and Health Administration (OSHA) Standards: OSHA sets workplace safety standards to protect workers from potential hazards during coating application and inspection. This includes guidelines on personal protective equipment (PPE), safe working practices, and exposure limits for hazardous substances.
International Standards for Coating Inspection
International standards provide a consistent set of guidelines that can be followed globally to ensure uniformity and quality in coating inspection. These standards facilitate international trade and ensure that coatings meet the same quality and performance requirements worldwide. Some significant international standards relevant to coating inspection are:
- ISO Standards: The International Organization for Standardization (ISO) develops standards related to coatings, corrosion protection, and inspection. ISO standards cover aspects like coating materials, surface preparation, application techniques, and inspection procedures.
- IEC Standards: The International Electrotechnical Commission (IEC) establishes standards for coatings used in electrical and electronic applications. These standards ensure the durability and performance of coatings in specific electrical environments.
Inspection Techniques and Tools
Visual Inspection
Visual inspection is a fundamental and essential technique in coating inspection. It involves visually assessing the coating surface for defects, irregularities, or imperfections. Coating inspectors use this technique to identify issues such as uneven coating, cracks, blisters, pinholes, discoloration, or contamination. The inspector relies on their expertise and training to evaluate whether the coating meets specified standards and requirements. Visual inspection often serves as a preliminary step before employing more specialized testing methods.
Non-Destructive Testing (NDT) Methods
Non-Destructive Testing (NDT) methods are employed to evaluate the integrity and properties of the coating without causing damage to the coated surface. These methods provide valuable insights into the coating’s thickness, adhesion, porosity, and other characteristics. Common NDT methods used in coating inspection include:
- Ultrasonic Testing (UT): Utilizes sound waves to measure coating thickness and detect anomalies within the coating.
- Magnetic Particle Testing (MPT): Detects surface and subsurface defects by applying a magnetic field and observing the response of magnetic particles.
- Dye Penetrant Testing (DPT): Identifies surface defects by applying a dye penetrant and then removing excess material to reveal defects.
- Radiographic Testing (RT): Uses X-rays or gamma rays to identify defects within the coating or substrate.
- Eddy Current Testing (ECT): Detects surface and near-surface defects by inducing eddy currents in the material.
The choice of NDT method depends on the specific requirements of the project, the type of coating, and the inspection objectives.
Coating Thickness Measurement Techniques
Accurate measurement of coating thickness is vital to ensure the coating meets the required standards and provides adequate protection. Various techniques are used to measure coating thickness, including:
- Magnetic Induction: Utilizes magnetic fields to measure the coating thickness on ferrous substrates.
- Eddy Current: Measures coating thickness on non-ferrous substrates by inducing eddy currents.
- Ultrasonic Measurement: Employs ultrasonic waves to determine coating thickness on a wide range of substrates.
- X-ray Fluorescence (XRF): Analyzes the X-rays emitted by a sample to determine the elemental composition and coating thickness.
Surface Preparation and Pre-Inspection Procedures
Surface preparation is a critical step in the coating process to ensure the adhesion and durability of the coating. Pre-inspection procedures are essential to assess the condition of the surface before coating, ensuring that it meets the necessary standards.
Cleaning and Degreasing
Cleaning and degreasing are fundamental steps in surface preparation. Before applying any coating, it’s crucial to eliminate dirt, oil, grease, or other contaminants from the surface. This can be achieved through various methods such as pressure washing, solvent cleaning, or abrasive blasting, depending on the surface type and the coating specifications. The goal is to create a clean and receptive surface for the coating to adhere to effectively.
Surface Profile Measurement
Surface profile measurement involves assessing the roughness or texture of the surface. The appropriate surface profile is crucial for achieving proper coating adhesion. Measurement tools like profile gauges or surface roughness testers are used to quantify the profile. The desired profile is typically specified in the coating manufacturer’s instructions, and it’s important to measure and document the surface profile to ensure it meets the required standards for the particular coating being applied.
Preparing Inspection Documentation
Before applying the coating, thorough documentation of the pre-inspection procedures is essential. This includes recording details of the cleaning and degreasing processes, surface profile measurements, any surface defects or irregularities, and other relevant information. Proper documentation provides a comprehensive record of the surface condition before coating, aiding in quality assurance and inspection processes. Inspectors use this documentation to verify that the necessary surface preparation steps have been completed according to the specified standards.
Coating Application Inspection
Coating Application Inspection is a critical aspect of ensuring the quality and integrity of coatings applied to various surfaces. Proper inspection during the coating application process is essential to ascertain that coatings meet specified requirements and adhere to industry standards. This section covers key aspects of coating application inspection:
Monitoring Coating Application Process
Monitoring the coating application process involves a systematic assessment of every stage during the application of coatings. This includes scrutinizing the preparation of the surface, application techniques, environmental conditions, equipment used, and the skills of the personnel involved. The goal is to ensure that the coating is applied in a consistent, uniform, and appropriate manner.
Key activities in monitoring the coating application process may include:
- Surface Preparation Assessment: Ensuring the surface is appropriately cleaned, abraded, and primed to facilitate proper adhesion of the coating.
- Application Technique Verification: Evaluating the application method (spraying, brushing, dipping, etc.) to confirm it aligns with the specified technique and achieves the desired coverage and thickness.
- Environmental Condition Checks: Verifying that environmental factors such as temperature, humidity, and ventilation are within the recommended range for effective coating application.
- Equipment Inspection: Checking the condition and calibration of equipment used in the application process, like spray guns or rollers, to guarantee accurate and consistent coating application.
Verifying Adherence to Application Specifications
To ensure the quality of the coating, it’s essential to verify that the application adheres to the specifications outlined in the coating plan or project requirements. These specifications may include details about coating type, thickness, curing time, adhesion, appearance, and other relevant parameters. Inspectors need to cross-check the actual application against these specifications.
Key components of verifying adherence to application specifications involve:
- Thickness Measurement: Using appropriate tools to measure the thickness of the applied coating and confirming it matches the specified thickness requirements.
- Adhesion Testing: Conducting tests to assess the adhesion strength of the coating to the substrate, verifying that it meets the specified standards.
- Visual Inspection: Examining the coating’s appearance to ensure it aligns with the desired finish, color, texture, and absence of defects as specified.
- Curing and Drying Validation: Confirming that the coating has undergone the necessary curing and drying processes as per the provided guidelines.
Identifying Common Coating Application Defects
Identifying and recognizing common coating application defects is crucial for addressing issues promptly and improving the overall quality of the coatings. Coating defects can adversely affect performance, aesthetics, and durability, making their identification vital during the inspection process.
Common coating application defects include:
- Blistering: Formation of bubbles or blisters on the coating surface due to inadequate surface preparation, moisture, or incompatible coatings.
- Cracking and Flaking: Formation of cracks or flakes in the coating, often due to improper adhesion, over-application, or inadequate curing.
- Sagging or Runs: Excessive application resulting in the coating running or sagging, affecting the finish and appearance.
- Orange Peel: A textured, uneven surface resembling the skin of an orange, typically caused by improper spraying techniques or inconsistent viscosity of the coating.
- Fisheyes: Circular or crater-like blemishes in the coating, usually caused by contamination or incompatible materials.
Conclusion
In conclusion, embarking on a Coating Inspector Course is a pivotal step towards mastering the intricacies of corrosion prevention and protective coatings. Through this educational endeavor, individuals enhance their knowledge and skills essential for ensuring the longevity and performance of various structures and assets. To further broaden one’s expertise and access comprehensive courses in this field, aspiring professionals should consider enrolling in programs offered by the esteemed CORCON Institute of Corrosion.
The CORCON Institute not only provides cutting-edge training but also ensures a solid foundation in corrosion management and effective coating inspection, enabling individuals to contribute significantly to the industry while advancing their careers. Investing in education through CORCON Institute of Corrosion will undoubtedly open doors to a wealth of opportunities and pave the way for a successful journey in the corrosion protection domain.
Image Reference: Freepik
Disclaimer: All trademarks, logos, and brand names are the property of their respective owners. All company, product, and service names used in this website are for identification purposes only. Use of these names, trademarks, and brands does not imply endorsement.